With the development of China's electric power industry and improve the level of technology, the voltage level used in the construction of power grids is also increasing, the technical requirements for transmission line tower products are getting higher and higher.
The main technology of the industry is as follows:
1, sampling technology sampling refers to the tower enterprise according to the design drawings and other technical information, based on technical standards, specifications, through the specialized sampling software for the actual simulation, the comprehensive consideration of the requirements of the production process and material requirements, the formation of the process for the workshop to use the processing technology process drawings of the process. Sampling is the premise and foundation of tower manufacturing, which is related to the correctness and accuracy of tower processing. The level of proofing is high or low, the suitability of the tower test assembly, conformity, etc. has a lot of influence, and at the same time affects the tower manufacturing cost of the tower enterprise. Power transmission tower sampling technology has gone through three stages: the first stage for manual enlargement, is sampling personnel according to the basic size of the tower design drawings, according to the principle of orthographic projection, in the sample plate according to the ratio of 1:1, through a series of line drawing to get the tower space structure of the planar unfolding map. The traditional sampling is more visual, and it is convenient and easy to check the sample plate and sample pole, but the sampling efficiency is low, the error and repetition workload is large, and it is difficult to deal with the special parts (such as the ground bracket, the tower leg V section and other complex structures), and it takes a long time to enlarge the sampling cycle and cultivate the sampling personnel. The second stage is hand-calculated sampling, which mainly utilizes the geometric method of solving triangles with plane trigonometric functions to calculate the actual dimensions and angles in the unfolding diagram of the tower parts. This method is more accurate than manual sampling, but the algorithm is complex and error-prone, and it is difficult to deal with some complex spatial structures. The third stage is computer-aided sampling, through the use of specialized sampling software for tower sampling work, that is, through the sampling software in the virtual three-dimensional space for the tower structure of the 1:1 model construction, so as to obtain the actual size of the tower components and the composition of the angle and other parameters, and the use of the software features to achieve the map and draw samples, print production lists and so on. Computer sampling can not only two-dimensional sampling, but also three-dimensional digital sampling, reduce the tower sampling calculation and calculation difficulty, improve the sampling accuracy and sampling efficiency, while also realizing the visualization of sampling, virtualization, concretization, intuitive. The development of computer-aided modeling software has gone through four stages, from the earliest two-dimensional coordinates of text data input, to three-dimensional coordinates of text data input, and then to three-dimensional coordinates of AutoCAD under the interactive input, and finally the development of three-dimensional entities under the interactive input of the work platform data. The technical core of the future three-dimensional sampling is the collaborative work and integration technology, three-dimensional sampling of the front-end and tower design connected to the back-end of the enterprise production information management system, and gradually to the enterprise-level information integration development, in order to achieve lean manufacturing, fast, flexible.
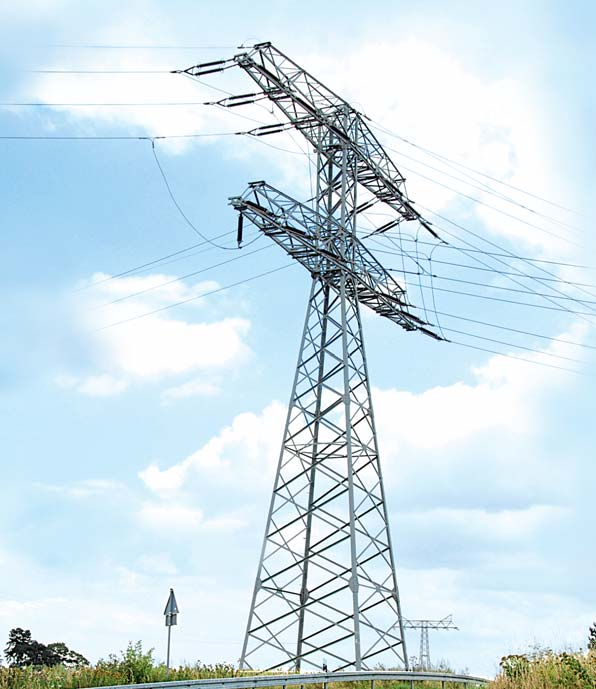
2, CNC equipment with the accelerated construction of power grids, the tower product demand has increased significantly, the transmission tower product models gradually increased, and the bar section from simple to complex, the bar section from simple to complex, the bar section from simple, the bar section from simple to complex, the bar section from simple to complex. Pole section from simple to complex, from single angle steel to double splicing angle steel, four splicing angle steel; from the development of steel pipe pole to lattice type tower; from the angle steel-based angle steel tower to the development of steel pipe, steel plate, steel and other mixed structures such as steel pipe towers, combined steel pole, substation structure bracket and so on. Tower products gradually to diversification, large size, high strength direction, promoting the technical progress of the tower industry, while bringing the tower processing equipment constantly updated and developed. With the continuous improvement of China's equipment manufacturing technology level, tower processing equipment, automation level gradually increased by manual processing equipment gradually developed to semi-automated processing equipment, automated processing equipment. Today, the tower processing equipment has been developed to CNC equipment, CNC joint production line, the degree of automation to obtain a substantial increase in the tower manufacturing key processes basically realize the automated production. At present, with the development of intelligent manufacturing technology, more and more multi-functional composite integrated processing equipment used in the tower industry, such as raw materials unmanned laboratory, multi-functional CNC angle production line, laser undercutting hole-making integrated processing equipment, heavy-duty laser pipe cutting machine, CNC double beam double laser composite processing equipment, six-axis tower foot welding robot, online monitoring system based on visual recognition, environmentally friendly Intelligent galvanizing production line and so on are more and more applied to the tower enterprise. The construction requirements of the digital workshop, and further promote the tower enterprise processing equipment for “dumb equipment” transformation, enhance its digitalization, informationization level. With the application of more advanced equipment manufacturing technology, tower processing equipment, the level of intelligence will be higher and higher, more intelligent tower processing equipment will be applied in the tower processing industry.
3, welding technology welding technology is a high-temperature or high-pressure conditions, will be two or two or more pieces of the parent material is connected to a whole and achieve inter-atomic bonding of the manufacturing process and technology. In the transmission line tower product manufacturing, many structures need to be welded to realize the connection between parts, welding quality directly affects the transmission line tower components of the force and tower set up and operation safety. Power transmission tower manufacturing industry is a typical small batch, multi-species, discrete processing. The traditional welding method, the use of manual scribing, manual grouping and spot welding fixed, manual arc welding welding, low efficiency, labor intensity of workers, welding quality by human factors have a greater impact. With the emergence of high-voltage transmission line towers (including large spanning tower) and other structural complex products, the welding process put forward higher requirements. The production of the above products is not only a large welding workload, the welding structure is more complex, the welding quality requirements are also higher, making the tower welding process gradually diversified. In the welding method, at present, China's power transmission line tower enterprises to CO2 gas shielded welding and automatic submerged arc welding, a small number of enterprises apply the tungsten argon arc welding process, and electrode arc welding is only used for positional welding or temporary welding of welding parts. Tower welding method from the traditional electrode arc welding, and gradually began to apply more efficient solid core and flux cored wire CO2 gas shielded welding, single wire and multi-wire submerged arc welding welding and other welding processes. In terms of welding equipment, with the development of intelligent equipment and rising labor costs in recent years, has given rise to a higher degree of automation of the professional tower welding equipment and welding process, such as steel pipe seam welding integration equipment, steel pipe - flange automatic assembly welding production line, steel pipe pole (tower) main automatic welding production line, angle steel tower foot welding robot system. In terms of welding materials, Q235, Q345 strength grade steel welding process has matured and solidified, Q420 strength grade steel welding process has become increasingly mature, Q460 strength grade steel welding technology has been successfully tested and applied on a small scale. In the large span tower, shaped steel pole and substation structure bracket project, cast iron, aluminum alloy, stainless steel and other materials welding also have a small number of applications, the tower welding technology puts forward higher requirements.
4, test assembly of transmission line tower test assembly is to test the transmission tower parts, components to meet the design and installation of the quality requirements in the pre-assembly before leaving the factory is galvanized before the overall installation of the tower products, the final test, the purpose of which is to test the overall installation of structural and dimensional characteristics of the product, and to ensure the quality of the product. It is the final inspection of the overall installation structure and size of the tower products before galvanization, and its purpose is to verify the correctness of the release and the conformity of the parts and components processing, and it is a key process before the products leave the factory. Therefore, usually choose a tower type of the first tower for trial assembly, in order to the tower for batch processing. For the sake of caution, some tower enterprises in a tower type after the first base tower trial assembly, the call height of different key parts of the tower, but also for local pre-assembly, in order to ensure that the site smooth group tower. The traditional test assembly of the physical assembly, general assembly time for each tower type is 2 to 3 days, the ultra-high voltage steel tower or complex structure of the tower, assembly and disassembly of the tower needs more than 10 days or longer, during which need to invest in more manpower and equipment, the tower manufacturing costs and processing schedule has a greater impact, and there is a greater risk of safety. With the development of three-dimensional sampling software, laser inspection technology, some tower enterprises to reduce costs and control safety risks, to carry out a three-dimensional digitization based on the virtual trial assembly research. Virtual trial assembly is the use of three-dimensional digital technology, the tower three-dimensional model and laser reconstruction technology combined, through the laser scanner scanning components to form a point cloud, the use of point cloud recovery components, and then use the assembly software to the components for virtual assembly, and finally after the assembly of the point cloud recovery of the three-dimensional model and the tower three-dimensional model for comparison and analysis, through the defects of early warning and other functions to detect the correctness of the components, so as to achieve the purpose of trial assembly. The purpose of assembly. At present, the technology has become more and more mature, the company's subordinate Zhejiang Shengda has been based on three-dimensional digitization of the virtual trial assembly of a useful attempt to accumulate a certain amount of experience and in the “Chongming 500kV transmission project Yangtze River crossing” in the successful application of the industry at the forefront. It can be predicted that with the continuous improvement and progress of the technology, the three-dimensional virtual test assembly technology of transmission tower will have a broad space for development.
5, intelligent manufacturing intelligent manufacturing is based on a new generation of information and communication technology and advanced manufacturing technology in-depth fusion, throughout the design, production, management, service and other manufacturing activities in all aspects of the new mode of production, with self-awareness, self-learning, self-decision-making, self-execution, adaptive functions, and so on. Production mode, thus becoming a hot spot in the manufacturing industry, which has attracted much attention. Transmission line tower manufacturing industry is a relatively small-scale industry, and has the characteristics of market demand diversification and product customization, to the promotion of intelligent manufacturing has brought some difficulty, the industry as a whole intelligent manufacturing started relatively late. However, tower companies have a high degree of enthusiasm to introduce new equipment with more functionality, more efficient integrated processing, enhance equipment automation, intelligent level, through the “machine instead of man”, to improve product quality and processing efficiency. Intelligent manufacturing is the road to the future development of the industry. At the same time, in the State Grid, the South China Power Grid and other downstream customers to promote the tower enterprises to accelerate the application of intelligent equipment and information technology, promote the visual identification technology, Internet of Things technology, intelligent manufacturing and other advanced manufacturing technology, accelerate the enterprise MES system, ERP system application, promote the tower manufacturing industry “soft”, “hard”, “hard” and “soft”. “” Hard ”combination of new models of development.
6, new tower materials transmission line tower is a typical steel structure, is the transmission and substation projects in the largest amount of steel-consuming power facilities. According to the different types of transmission line tower products, the main types of raw materials are also different, of which, the main raw materials for the angle tower hot-rolled equilateral angle steel, hot-rolled steel plate; steel tower main raw materials for the LSAW pipe, forging flange, hot-rolled equilateral angle steel, hot-rolled steel plate; the main raw materials for the hot-rolled steel pole; substation structure bracket main raw materials for the steel, steel, steel pipe. For a long time, China's power transmission towers with a single variety of steel, strength is not high, the material to Q235B, Q355B carbon structural steel. The growing demand for the construction of ultra-high voltage projects has promoted the diversification of steel varieties used for towers, large-scale specifications, and high quality of materials. At present, Q420 grade angle steel, steel plate has been widely used in the angle steel tower, steel pipe tower of the UHV project, which has become the main material of the transmission tower, Q460 grade steel plate, steel pipe in some of the steel pipe tower, steel pipe pole project began to pilot and large-scale application; Angle steel material specifications have reached ∠ 300 × 300 × 35mm (side width of 300mm, the thickness of 35mm of the equilateral angle steel), so as to realize Angle steel tower to single-limb angle instead of double splicing angle steel, double splicing angle steel instead of four splicing angle steel, simplified the tower structure and processing technology; in order to adapt to the requirements of the low temperature in winter in the northern part of our country or plateau area, the higher quality grade (C grade, D grade) of the steel has also begun to be widely used in the tower products of the transmission line. With the continuous development of design technology and material technology, transmission line tower material diversification trend is obvious, such as ductile iron pipe poles instead of cement poles and part of the steel pipe poles used in agricultural or urban network distribution lines, composite materials have been used in different voltage levels of transmission lines in the tower crossbar. In order to solve the conventional tower hot dip galvanizing higher cost, environmental pollution, the development of atmospheric corrosion-resistant cold-formed weathering angle, hot-rolled weathering angle, weathering fasteners, etc.; cast iron parts, aluminum profiles, stainless steel and other materials in the application of transmission line towers are also trying to
7, anticorrosive technology transmission line towers due to year-round exposure to the outdoor environment, susceptible to the erosion of natural environments, and therefore the need for the Anti-corrosion treatment of the product to improve its resistance to erosion, prolong service life. At present, China's power transmission line tower enterprises generally use hot dip galvanizing process to achieve product anti-corrosion. Hot dip galvanizing is the surface by cleaning, activation of steel products immersed in molten zinc liquid, through the reaction between iron and zinc and diffusion, in the surface of steel products coated with zinc alloy coating with good adhesion. Compared with other metal protection methods, hot-dip galvanizing process has good performance in the combination of physical barrier and electrochemical protection of the coating, and it has significant advantages in terms of the bonding strength between the coating and the substrate, the denseness, durability, maintenance-free and economy of the coating, as well as its adaptability to the shape and size of the products. In addition, the hot dip galvanizing process also has the advantages of low cost and beautiful appearance, so the advantages in the field of transmission line tower manufacturing is obvious, is currently the mainstream tower product anti-corrosion technology. In addition to hot dip galvanizing process, for some oversized components, usually also use hot spray zinc or high-pressure cold spray zinc process, with the environment and quality requirements, matte galvanizing, zinc aluminum magnesium alloy galvanizing, bimetallic anti-corrosion coatings and other new anti-corrosion technologies are also applied in the project, tower anti-corrosion technology will be diversified development!
Post time: Jan-10-2025